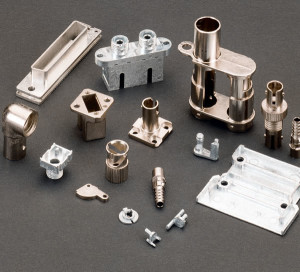
Zinc Die Cast Advantages
Today’s zinc casting alloys are strong, durable and cost effective engineering materials. Their mechanical properties compete with and often exceed those of cast aluminum, magnesium, bronze, plastics and most cast irons. These characteristics, together with their superior finishing capabilities, make zinc alloys the unquestioned material choice for the 21st century, because they’ll save you time and money.
Assembly Operations are Reduced
Entire assemblies can be cast as a single unit, eliminating the need for expensive manual assembly operations.
Less Material is Required
Zinc’s superior casting fluidity, strength and stiffness permits the design of thin wall sections for reduced weight and material cost savings.
Machining Operations are Reduced
Due to the superior net-shape casting capability of zinc diecast alloys, machining can be eliminated or drastically reduced
Faster Production and Extended Tool Life
Die-cast manufacturing rates for zinc are much faster than for aluminum, or magnesium. Coupled with a tool life often exceeding 1 million casting cycles, tooling and machine usage charges are dramatically reduced.
Going Green
Zinc takes less energy to melt because its melting point is only 787.2°F, whereas aluminum’s melting point is 1,221°F. This also gives zinc an advantage over aluminum on the recycling end because it takes less time and energy to melt zinc down than aluminum. Over the course of 2 cycles, zinc would save over 800°F worth of heating energy over aluminum.
Smoother Surface, Better Finish
Zinc castings come out with a much smoother surface than aluminum castings, which makes them easier and less tricky for finishing. Aluminum castings usually have to be buffed before they can be finished which represents a significant increase in processing costs.
Zinc Die Cast – Zamak Die Casting Manufacturing